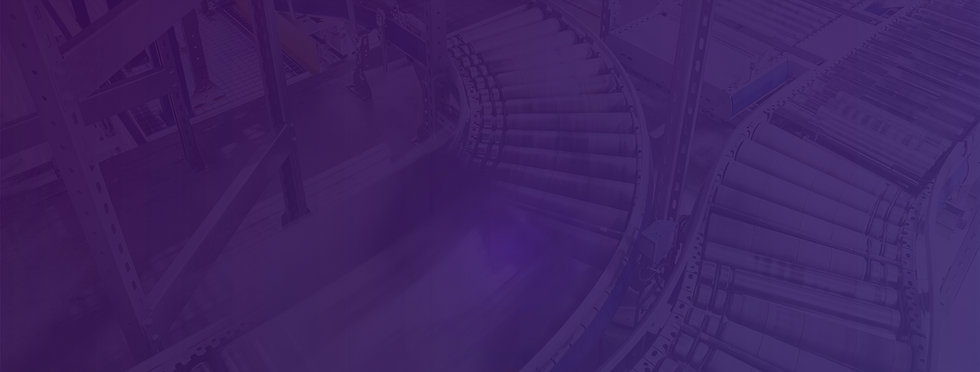
System Process Data
The mHub module for process data control
DATA CONTROL FOR EFFICIENCY
Predefined quality to reduce costs
Statistical process control is the process of tracking and verifying measurement data from the production process in real time. To address the user's predefined quality standards, it is possible to setup upper and lower process value limits, which leads to a complete production-halt when limits are reached. This helps avoiding unnecessary costs due to produced scrap.
WHERE IT IS USED
Use cases & business units

Production
Maintenance
Quality
WHY SYSTEM PROCESS DATA
Advantages overview

QUALITY ASSURANCE
Through live data tracking, process limits violations detected in real time and measures can be initiated.

TRACEABILITY
Full traceability to the system process data is essential, especially with high-quality production standards.

ARCHIVING
AND REUSABILITY
Process data parameters can already be transferred to the controller when the system is commissioned.

SECURE KNOWLEDGE
Knowledge about plant process data no longer personified, but accessed any time. Training and
commissioning drastically reduced.

STANDARDIZATION
New systems and production lines can be put into operation efficiently thanks to standardized interfaces for quality testing and operating procedures.
MODULE DESCRIPTION
What is our System Process Data?
The System Process Data module combines traditional statistical process control as a quality control method. It features process data logging for product accountability, as well as guards against changes to preset program parameters. Based on the protocol standards OPCUA, MQTT and REST, you can connect any production system and check, archive and analyze their process data in real time. In addition, it forms the basis for the creation of solutions based on artificial intelligence (AI). Quality and efficiency issues can be checked against program parameter changes. The module consists of the following 3 functions:

Statistical Process Control (SPC)
Automated alarms can be triggered in the event of violations via defined process limits and parameters. These can either have human recipients (email, SMS, WhatsApp and text to speech) or trigger other processes using machine interfaces via OPCUA, MQTT and REST calls.

Process Data Logging
This is used in the case of responsibility towards the customer in quality-sensitive process steps. It serves the obligation to prove production process accuracy by providing process data. It is also used to track products in the event of possible product recalls. Furthermore, it can also serve as a training model for AI to identify correlations.
The logging workflow in the system process control describes the process-data logging based on unique components' serial numbers (also called spimes). It also analyzes and exports them in the event of product reclamations and recalls. Based on the data, you can examine why certain parts are failing and how you can improve your process parameters by defining better intervention limits.

Program Guard
The program monitor can be used to check program changes against parameters defined for a product on the production system in the OEM standard for the initial sampling process. With the Program Guard, the predefined programs for the production system could be transferred automatically when production starts. All parameter changes made by users on the machine can be tracked and supervisors can be notified. Program defaults can easily be restored. Quality and efficiency issues can be checked for correlations with changed program parameters.